Resistance of an electronic device to vibration tests: How to design a suitable mechanism.
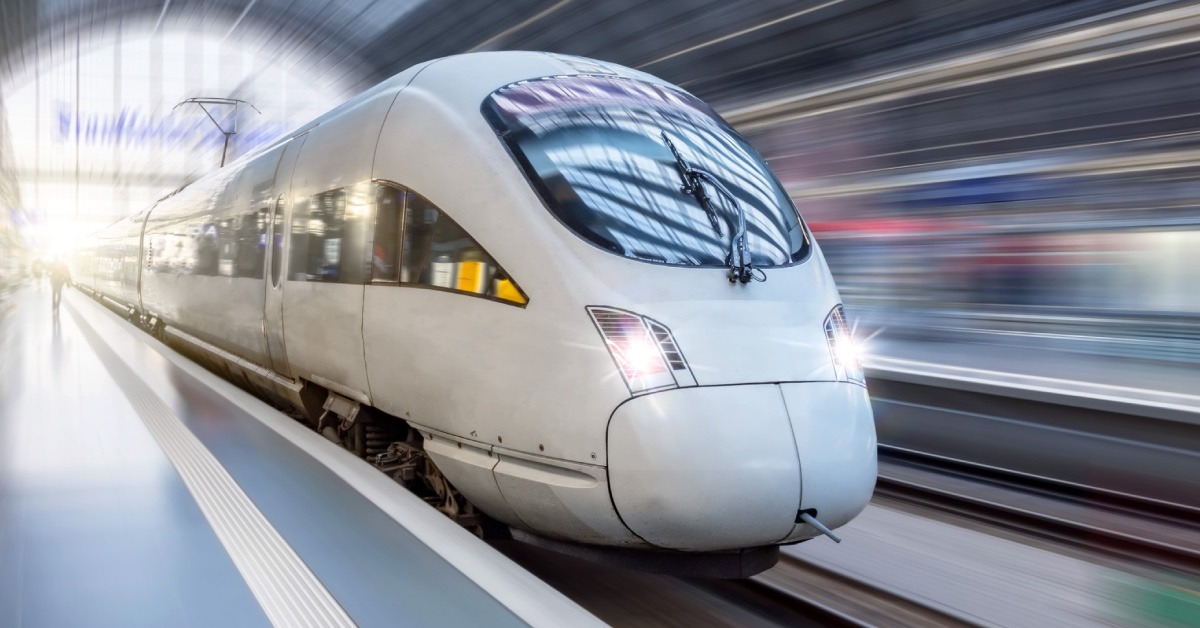
What does it mean to pass a vibration test and obtain EN 61373 certification for your product in the railway sector?
For us, it means immersing yourself in the life of your product and building a constant dialogue between mechanics and electronics.
This is why elmec srl technicians have participated in functional tests for resistance to vibration regimes typical of a system moving on rails.
What did we learn?
What are the elements to be evaluated in the design phase?
Before we find out, let’s see how a vibration test is typically carried out.
The vibration test is carried out with a machine (similar to a sound box) that creates vibrations (frequencies) to simulate the life of the product mounted on a train.
The test is divided into three phases:
Frequency (from 5hz to 150hz)
- Random vibration (continuously changing frequencies randomly)
- Sinusoidal mechanical vibration
- Shocks (Shock) with 5Gs of acceleration
Tests are performed along the three axes X, Y, Z of the part.
The test is generally carried out on a single sample, which must be switched on and in operation for the entire duration (which can be several weeks).
Critical points are highlighted in particular by the generation of frequency resonance situations, which must be analysed and resolved.
Any subsequent mechanical or electronic modifications involve repeating the test on the modified sample to certify that it can also pass the test again.
Designing the mechanical container, anticipating as much as possible the resolution of the critical points, therefore means not wasting time and energy in repeating long and costly tests.
So what are the critical variables that must be taken into account when designing the mechanical enclosure?
First of all, it must be said that there is no single perfect recipe, as each product has its own specific behaviour resulting from many variables at play.
There are, however, certain tricks that can be decisive for success. Let’s see which ones:
- Rigidity and centre of gravity: One of the first and fundamental variables concerns the arrangement of the mass. The more the centre of gravity of the device is positioned centrally, the more it will be able to be integral with the moving vehicle and thus have a more predictable behaviour to vibrations. Therefore, if possible, avoid masses placed unbalanced on the volume of the product and always bear in mind that stresses are induced and tested on the 3 axes X,Y,Z.
- Geometry of the product in relation to the attachment points: The arrangement of the fixing points of the product on the support that will house it is another fundamental variable. The more evenly the points are arranged across the surface and close to critical areas (the heaviest, for example), the more predictable and less burdensome the behaviour will be.
- Fewer components, fewer variables: In addition to the arrangement of connection points, the type and quantity of fastening points also make a difference; not only between the different mechanical parts involved, but also between mechanics and electronics. In general, the fewer parts involved, the fewer potential critical points. Specific attention must be paid to the arrangement and fixing of cables, connectors and the direct interconnection between the various boards.
- Combination of materials used: The choice of construction materials can determine the success of vibration tests. Relying on materials with good mechanical properties combined with lightness, such as aluminium, is often the winning choice. Using several different materials with different specific weights makes it more difficult to balance the product’s centre of mass. This is why unibody mechanical shells are often used.
- Direct contact between parts: When choosing the materials used, the potential effect of direct contact between different parts during a vibration regime must be taken into account, typically the presence of display glass.
- The fixture: An equally strategic variable is the design of the fixture that houses your product on the test machine, simulating the conditions of installation on the moving vehicle. The fixture must be a single body as much as possible with the machine and the product, so as not to amplify the conditions that would make the test more onerous. It must be as neutral as possible.
Designing a high-performance and reliable device to support your on-board electronics over time is a constant challenge for our engineers.
We look forward to learning about your next new product and giving you our support.